Justin Rowlett,BBC Local weather Editor , @BBCJustinR
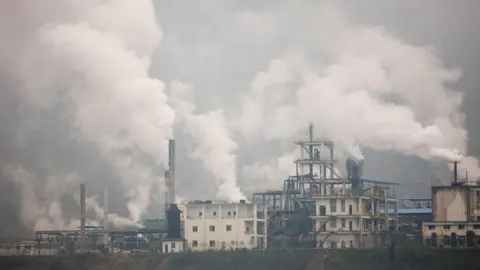
Scientists say they’ve discovered a strategy to recycle cement from demolished concrete buildings.
Cement is the commonest development materials within the trendy world, however it’s also a serious supply of greenhouse fuel emissions.
This is because of chemical reactions whenever you warmth limestone to excessive temperatures by burning fossil fuels.
Recycling will drastically scale back the carbon footprint of cement. In the event that they change to electricity-powered furnaces, and use renewable power like wind and photo voltaic as an alternative of fossil fuels, it might imply no greenhouse gases can be launched, the researchers say.
And that may be a giant deal. Cement types the muse of the fashionable financial system, actually and figuratively.
It’s what binds the sand and combination in concrete, and concrete is the second most used materials on Earth after water.
Additionally it is a serious driver of local weather change. If cement have been a rustic, it will be the third largest supply of emissions after China and the US, accounting for 7.5% of human-made CO2.
The issue is the uniquely polluting chemistry of the fabric.
It’s made by heating limestone to 1600 Celsius in big kilns powered by fossil fuels.
These exits are just the start. Warmth is used to drive carbon dioxide from the limestone, forsaking a cement residue.
Add these two sources of air pollution collectively and it’s estimated that for each ton of cement, a few ton of carbon dioxide is produced.
A workforce of scientists from the College of Cambridge has discovered a clear strategy to take away these emissions.
It exploits the truth that you may reactivate used cement by re-exposing it to excessive temperatures.
The chemistry is effectively established, and has been accomplished at scale in cement kilns.
The breakthrough is to show it may be accomplished by piggybacking on the warmth generated by one other heavy business – metal recycling.
Once you recycle metal, you add chemical substances that float on the floor of the molten steel to forestall it from reacting with air and creating impurities. This is called slag.
The Cambridge workforce discovered that the composition of the cement used is nearly similar to the slag utilized in electrical arc furnaces.

They’re trialling the method in a small-scale electrical arc furnace on the Supplies Processing Institute in Middlesbrough.
The BBC was current when the primary excessive grade, or “Portland”, cement was produced.
They’re calling it “electrical cement” and describe the phenomenon as a world first.
Lead scientist, Cyril Dunant, instructed the BBC that it might allow the manufacturing of zero-carbon cement.
“We’ve proven that the excessive temperature within the kiln reactivates the previous cement and since electrical arc kilns use electrical energy, they are often powered by renewable power, so the entire cement making course of is decarbonised, ” he stated.
He stated it additionally makes recycling metal much less polluting due to the excessive carbon value of creating the chemical substances at present used as slag.
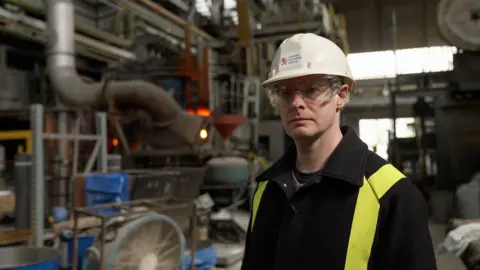
Mark Miodonik, professor of supplies and society at College School London, described the Cambridge workforce’s strategy to combining cement and metal recycling as “genius” and believes that, if it may be made to work profitably at scale, So this may result in an enormous discount. exit
“Can it compete with the present infrastructure that could be very quickly pumping cement into our lives”, he asks.
“Cement is already a billion greenback business. That is David and Goliath we’re speaking about right here.
Electrical cement is predicted to be cheaper to fabricate as a result of it makes use of primarily waste warmth from the metal recycling course of.
Spanish firm Celsa will attempt to replicate the method at its full-scale electrical arc furnace in Cardiff this week.
The Cambridge workforce estimate that, given present charges of metal recycling, their low-carbon cement might produce the equal of 1 / 4 of UK demand.
However using electrical arc furnaces is predicted to extend sooner or later, probably permitting extra “electrical cement” to be produced.
And, after all, the method could be duplicated everywhere in the world, probably lowering cement emissions dramatically.
